Industry
About the project
Product quality is a key component of automotive production, no matter the stage. Through several projects with our client, we aimed to kick-start efficiency by creating a comprehensive, intuitive system for work orchestration and communication with service partners, as well as a system for tracking feedback and product quality.
Challenge
In order to best track and orchestrate aftermarket services, our client required an advanced system. This system needed to integrate easily into the client’s existing ones to allow for creation and tracking of customer requests, inventory management, and report generation. It would then be used to communicate whether a request has been completed or to highlight additional steps needed to complete the process.
In addition, the client lacked processes for dealing with product quality and client feedback, particularly when it comes to aftermarket automotive safety and legislation. An inefficient manual system prevented access to much needed data, which caused issues with transparency and feedback.
The automotive aftermarket, it can be argued, is just as important as the entire production cycle. Efficiency in this area is vital—particularly when considering the impact on the end user. Whether that simply means prompt arrival of the vehicle into the customer’s hands or, more critically, the gathering and processing of complaints and concerns, the right processes must be in place. We’re honored to work together with the client on this project towards overall customer safety and satisfaction.
– Ivan Mandić
Engineering & Delivery Lead in Automotive at HTEC Group
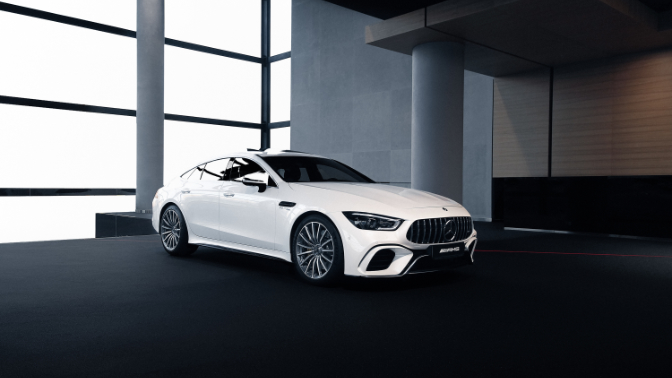
Success
Our solution, a core system for aftermarket sales, will drastically improve efficiencies within the client’s aftermarket operations. The time needed to process customer requests will be reduced, while inventory accuracy will be improved. The client will be able to generate more detailed and accurate reports, allowing for much clearer visibility into request statuses.
A secure tool was also implemented, which now allows for information logging of urgent customer feedback. This includes a workflow covering everything from pre-production, production, to aftermarket, including corrective actions and solutions. In addition, a product quality system will also be implemented to handle less critical reports.
By reducing the margin for error and improving communication between the client and its service partners, customer satisfaction has improved. In addition, through the implementation of a product quality management system, manufacturing errors can be caught in time to prevent serious incidents on the road, thus contributing to road safety.
To find out how we can drive your automotive industry forward, visit this page or feel free to contact our team directly.